Tufts Rocketry Team: IREC Spaceport America Cup 2024
The IREC Spaceport America Cup is the largest collegiate rocketry competition in the world, with 121 teams competing against each other in 2024. This year was Tufts’ first entry to Spaceport America, as well as our first competition of any kind. We competed in the 10k COTS division (a 10,000 foot target altitude and a Commercial Off-The-Shelf motor), taking our 8.8-pound payload to 9,462 feet and recovering it unscathed. The successful launch and our technical documentation efforts earned us 34th place out of 121, amongst the best for new teams.
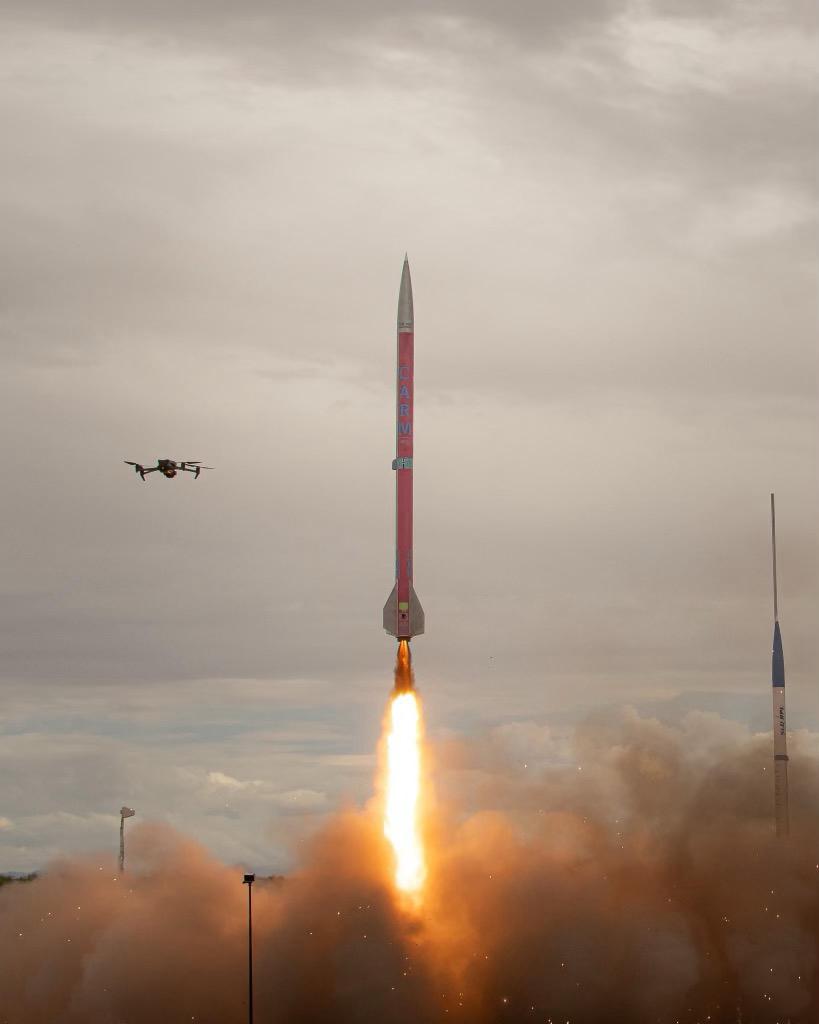
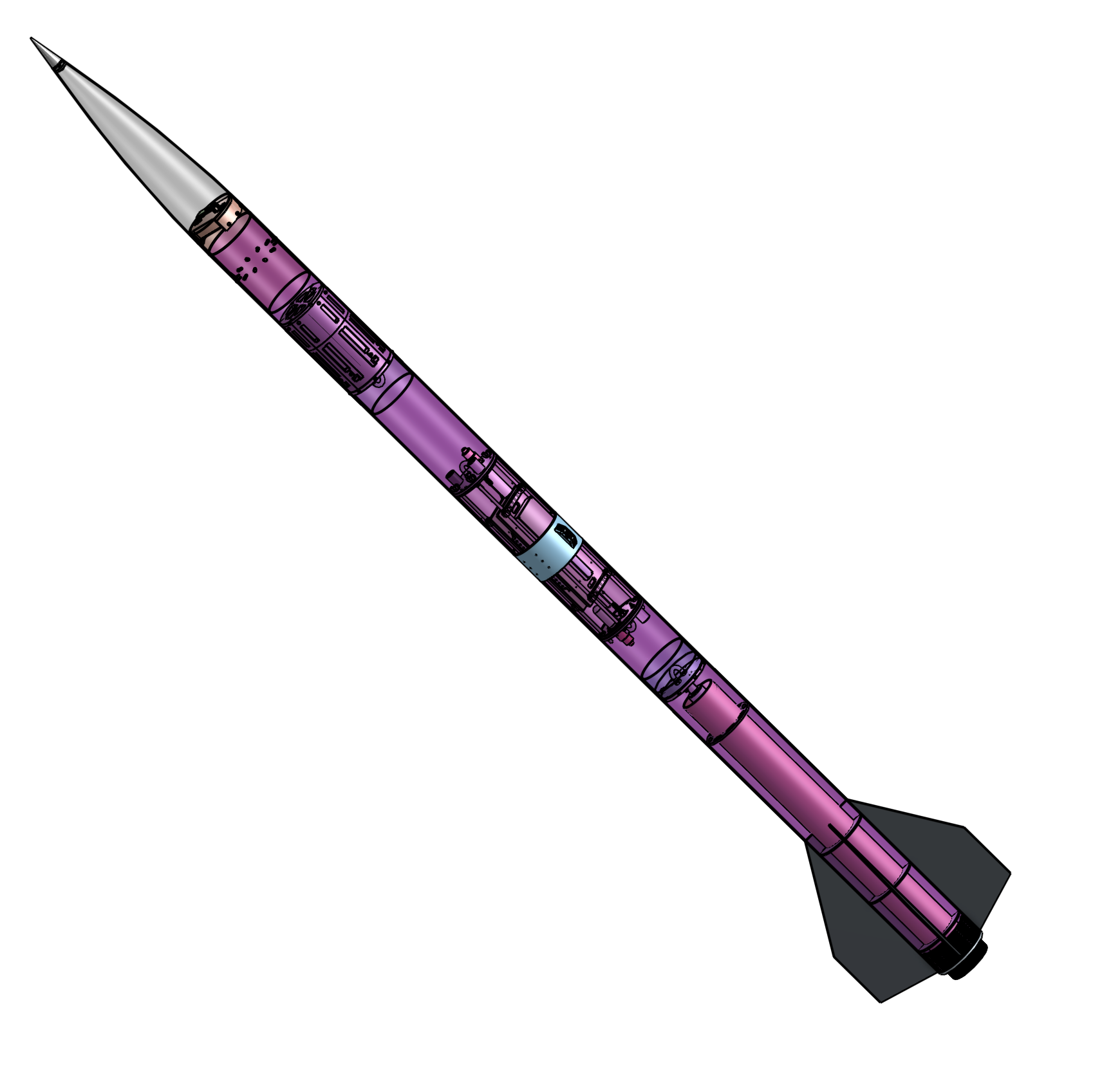
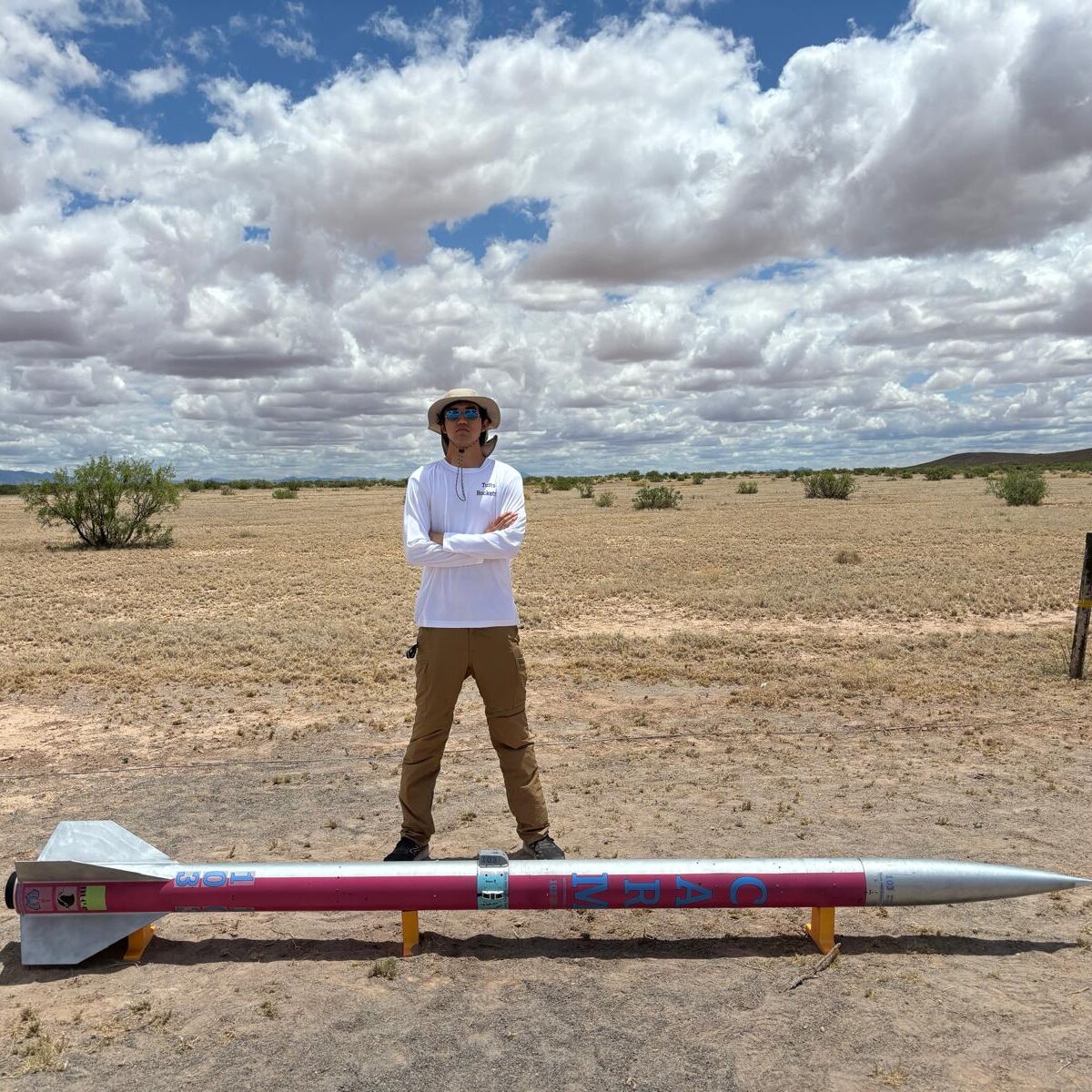
As Mechanical Team Lead for CARM (short for CubeSat-Adorned Rocketry Masterpiece, sharing a name with the beloved Tufts dining hall), my responsibilities were as such:
- Developing dimensionally accurate, professional CAD models and engineering drawings in OnShape.
- Ensuring parts would withstand the mechanical and thermal stresses of launch and recovery; this includes Ansys simulations, fin flutter calculations, and materials research, as well as learning from three test flights.
- Organizing and assisting in the manufacturing of airframe and payload components, such as the fiberglass airframe with its custom layup, 3D-printed and laser-cut parts for the avionics bay, and aluminum components made by CNC tools.
- Educating and engaging with my team, which was almost entirely freshmen engineers in the beginning.
- Coordinating with my fellow team leads to ensure our designs met the needs of the Electrical, Avionics, Propulsion, and Recovery teams.
- Prior to graduating, establishing new positions (Airframe, Metalworking, and Theoretical sub-team leads to assist my successor) and setting up an extended transition period to assist the next Mechanical Team Lead.
CARM is, without a doubt, the most complex and time-intensive project of my undergraduate education. It improved my technical skills in creating readable, organized CAD assemblies, thoughtfully designing and interpreting simulations, and manufacturing with a wide range of materials. My prowess as a communicator and leader was enhanced by leading meetings for the Mechanical team, talking with members of leadership to discuss our plans, documenting our work, and presenting our progress to mentors, professors, and sponsors at design reviews.
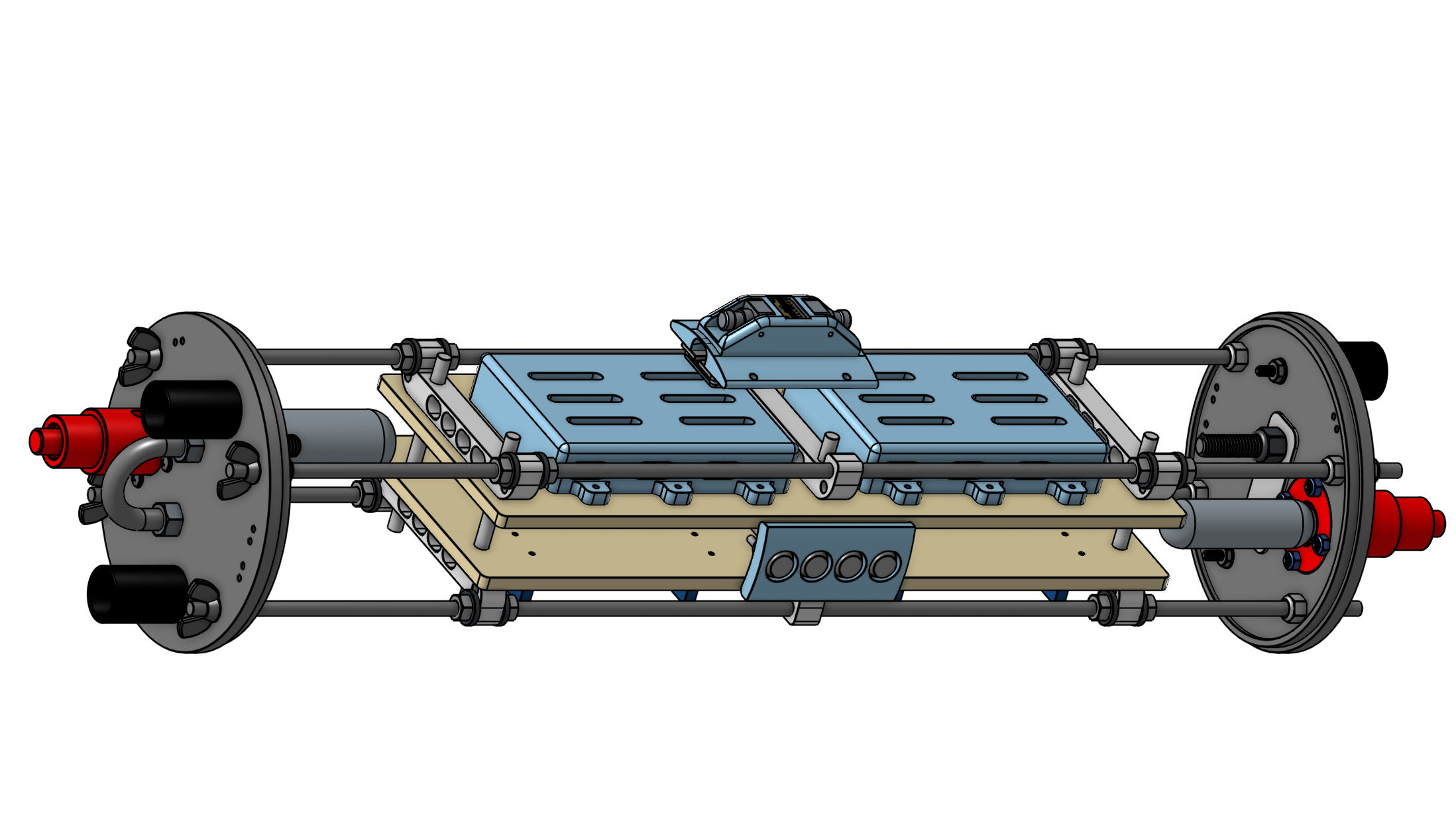
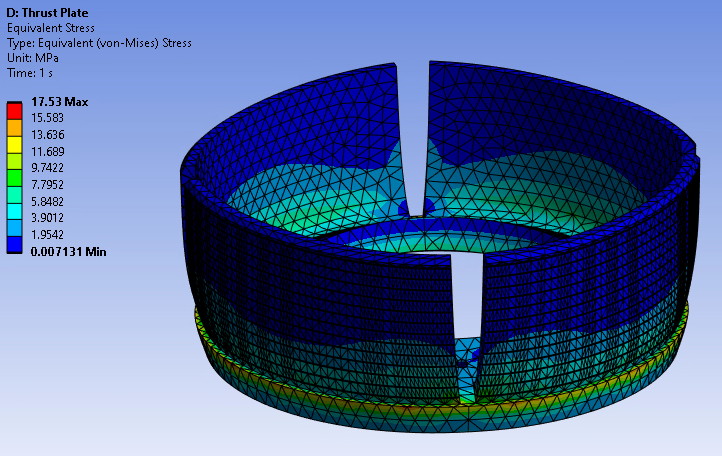
For a deeper dive, I highly recommend reading the full CARM documentation below. Special thanks to Nico Moldovean, May Wildgrube, Daniel Opara, Cisco Hadden, Rachel Bonnano, Ben Fisher, and everyone else on the rocketry team for your support and friendship. Everything I accomplished as Mechanical Lead would have been impossible without you.
L2 Certification: Go Blue!
Motor: Aerotech J425R-14A, 38mm, 452N peak thrust, 676Ns impulse
Dimensions: 157cm length, 10.2cm diameter, 2.6 kg fully loaded
Certification Details: May 2025, St. Albans, VT; 40/40 score on NAR written exam
Key Improvements over L1:
- Small fins with low sweep angle to minimize risk of damage on landing
- Compensated for small fins with a heavy nosecone to increase stability
- Doubled the fin assembly thickness
- Calculated ejection charge required to ensure chute deployment
- Swapped cardboard airframe for vulcanized cellulose to enhance strength and impact resistance
- Used epoxy, clamps, and masking tape to create robust, well-fitted connections to the airframe
- Used a steel retainer and bolts plus threaded inserts to contain motor
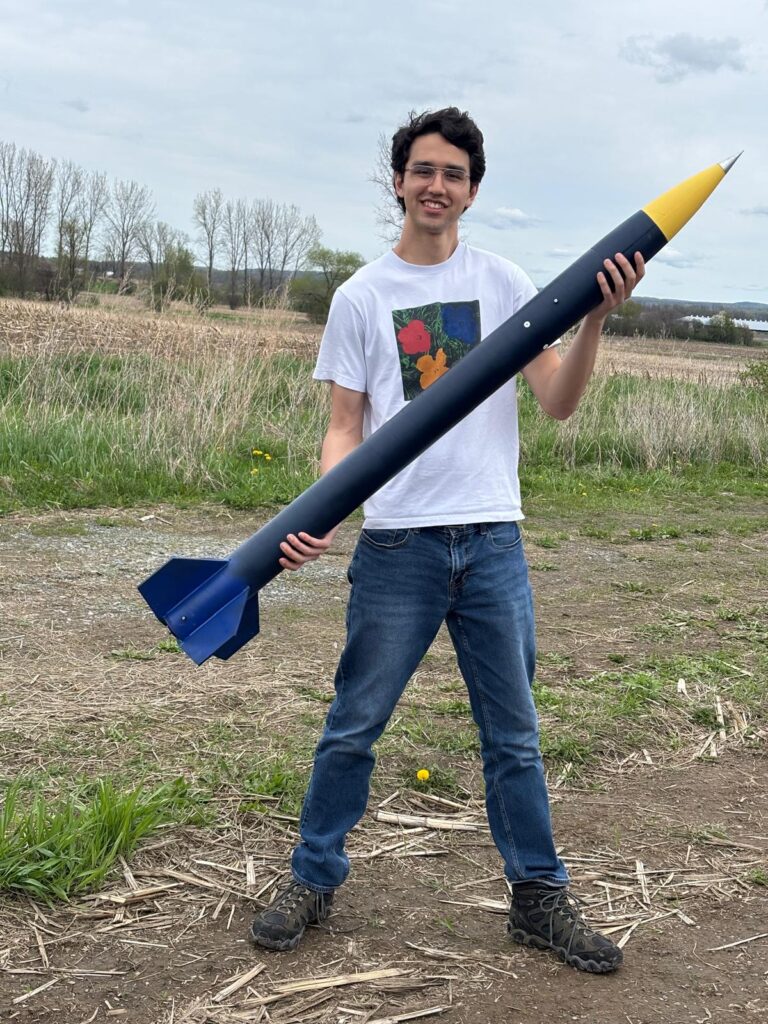
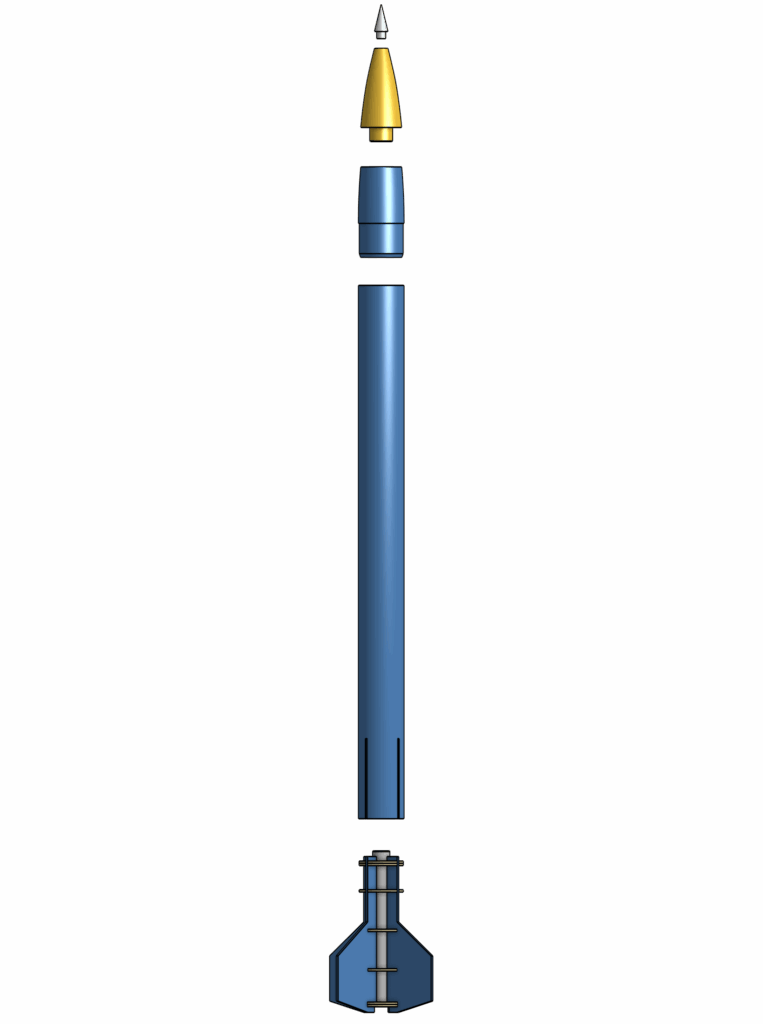
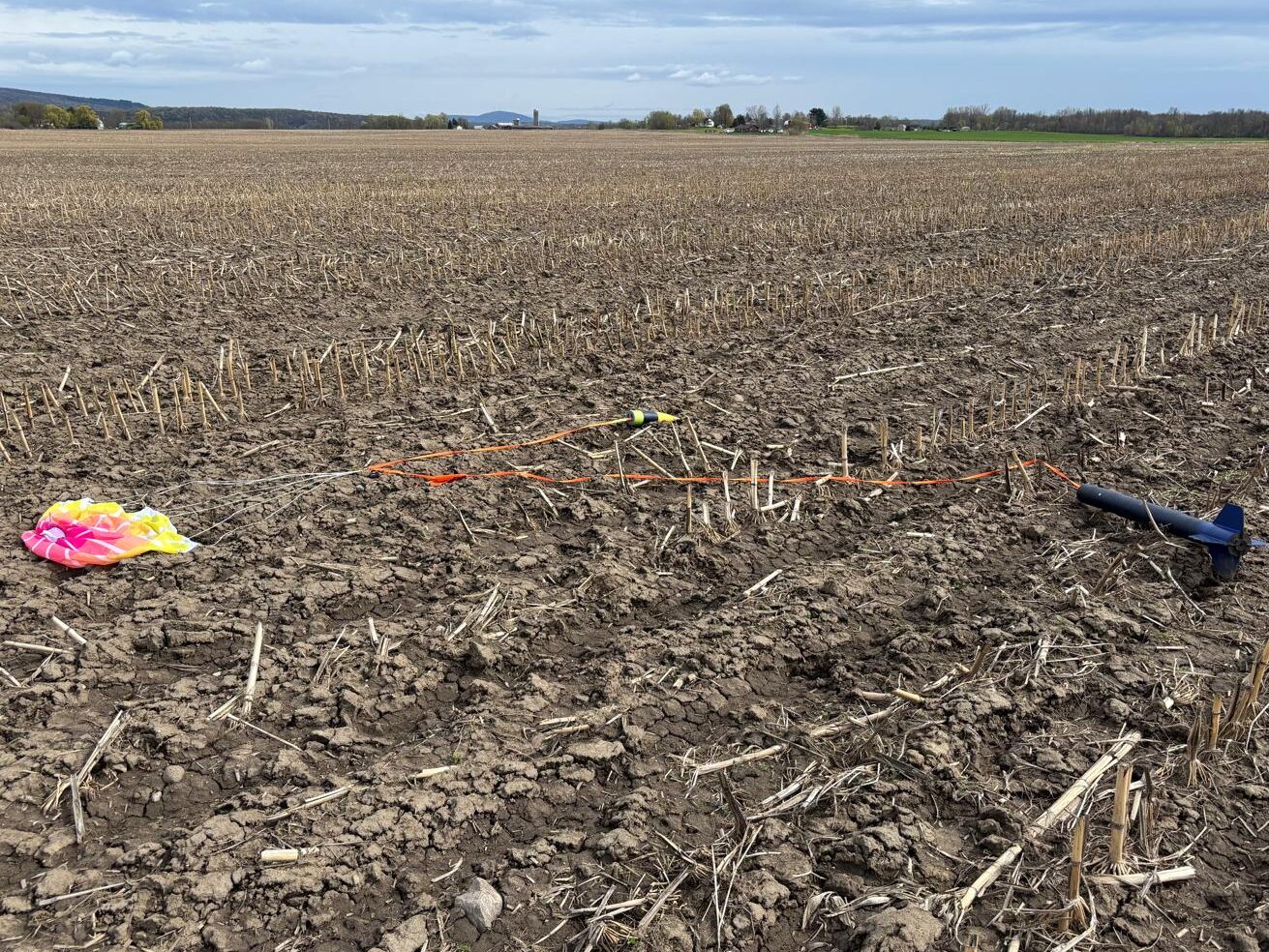
The rocket was designed using the open-source software OpenRocket, after which it was finalized in OnShape. After calculating the center of pressure in OpenRocket and experimentally determining the center of gravity, the stability of the rocket was 1.7 (meaning CP is 1.7 body diameters behind CG; stability between 1 and 2 is ideal).
On the first launch, the chute failed to unfurl properly, a common and occurrence when using a Jolly Logic Chute Release. However, the rocket’s robust design meant that no irreparable damage was sustained by the hard landing, and its second flight was a success after a quick motor reload and setting the chute release to a higher altitude to allow for more time to unfurl.
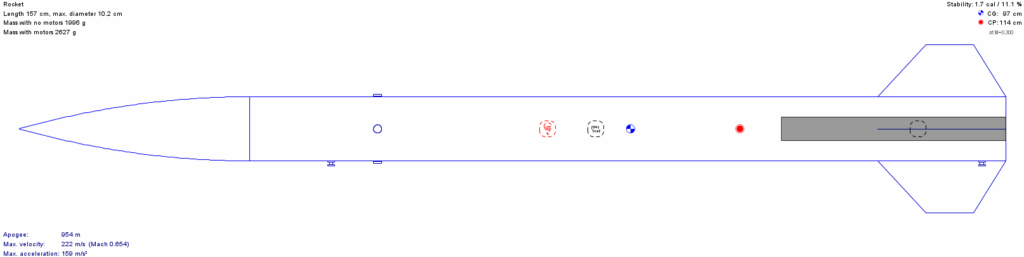
L1 Certification: Golden Age
Motor: Cesaroni H200-14A, 29mm, 303N peak thrust, 261Ns impulse
Dimensions: 112cm length, 7.9cm diameter, 1.1 kg fully loaded
Certification Details: October 2022, West Kingston, RI
My L1 certification rocket was a critical first step into the world of high-power rocketry. The process introduced me to basic rocket construction techniques, software like OpenRocket, and principles of rocket design such as stability and recovery systems.
While Golden Age’s first flight was a success, earning me my L1 certification, I had to admit its design was primitive in many ways. The structure was relatively flimsy and the fin assembly was poorly fitted to the airframe, among other concerns. The lessons I learned from this simple first flight translated to an excellent L2 certification rocket and even my work on Tufts’ successful competition rocket a year later.
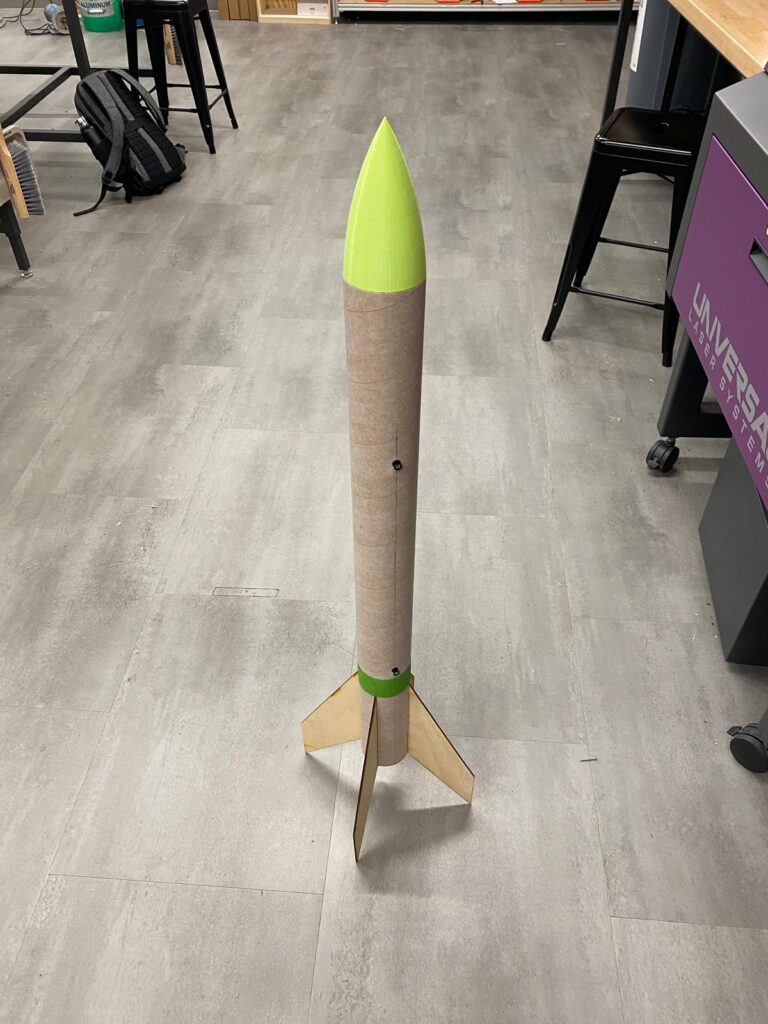
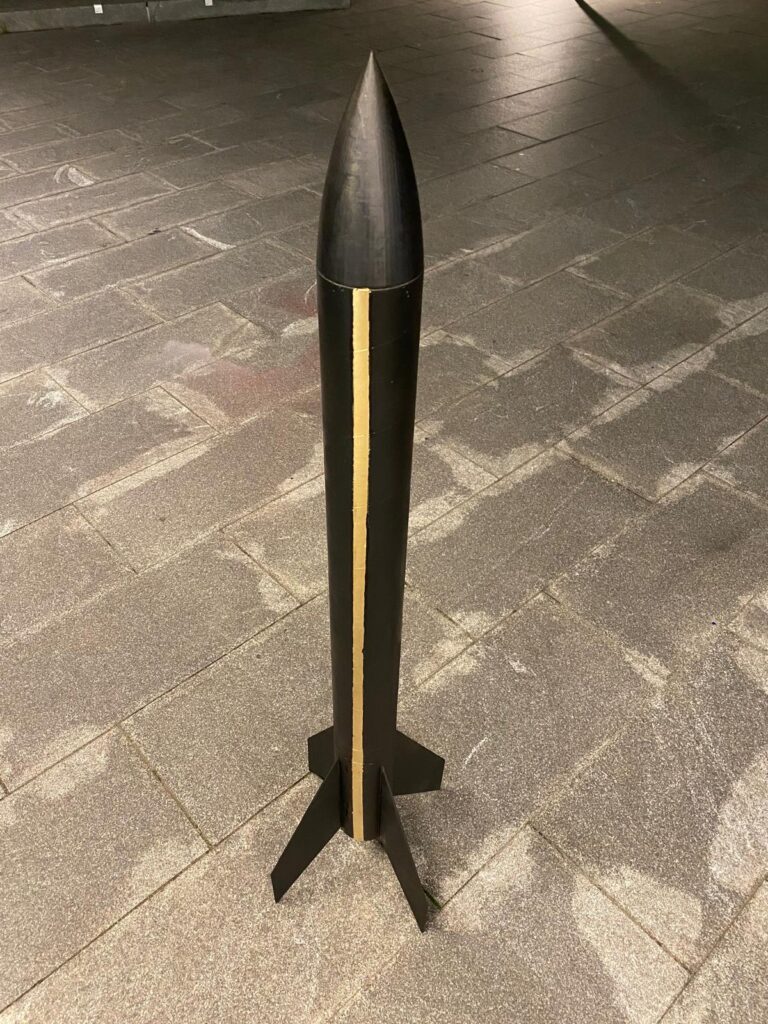
Future Projects
- First Dual Deploy L2-class Rocket
- First Dual-Stage Rocket
- First L3 Attempt (M-Class: 10,240 Ns or greater of impulse)